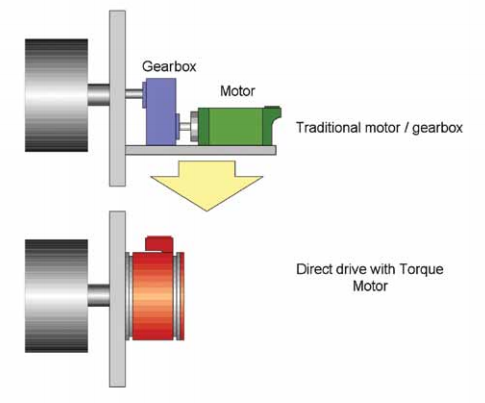
Let’s start with the definition of direct drive. In a conventional system, the moving elements of a machine are connected to the motor via gears, belts and couplings:
Direct drive motors:
By contrast, in a direct drive system the rotary or linear motor is connected directly to the load. Here are the top advantages gained by doing this:
More Confident Engineering and Delivery
- Precision: With the motor coupled directly to the load, gearbox backlash and belt compliance is no longer degrading your repeatability.
- Reliability: For when it absolutely, positively must keep working overnight. When mechanical power transmission components are eliminated by using a direct drive solution, there are fewer things to fail. You can even take it one step further with a cartridge motor design and eliminate bearings from the motor altogether.
- Size Weight and Power (SWaP): Bigger is not always better. When couplings, gearboxes and other power transmission components are eliminated, the power density of the system increases. Pack more power into the same package size, or keep the same power and reduce size. Take it to the next level and eliminate the motor housing as well by embedding a frameless direct drive motion solution.
- Speed: Direct drive technology can help maximize the productivity of your machine. The higher accelerations enabled by direct drive technology can shave precious milliseconds from your index times and increase your throughput.
- Profit: Reduced maintenance and unscheduled downtime costs along with enhanced efficiency and capability add up to greater value delivered to the customer.
Author: Nimble Electric Experts
Nimble Electric offers a full range of diversified products & applications including custom-engineered high precision Torque Motors, Direct Drives etc for demanding environments.